Not a review - but very good read.
www.caranddriver.com
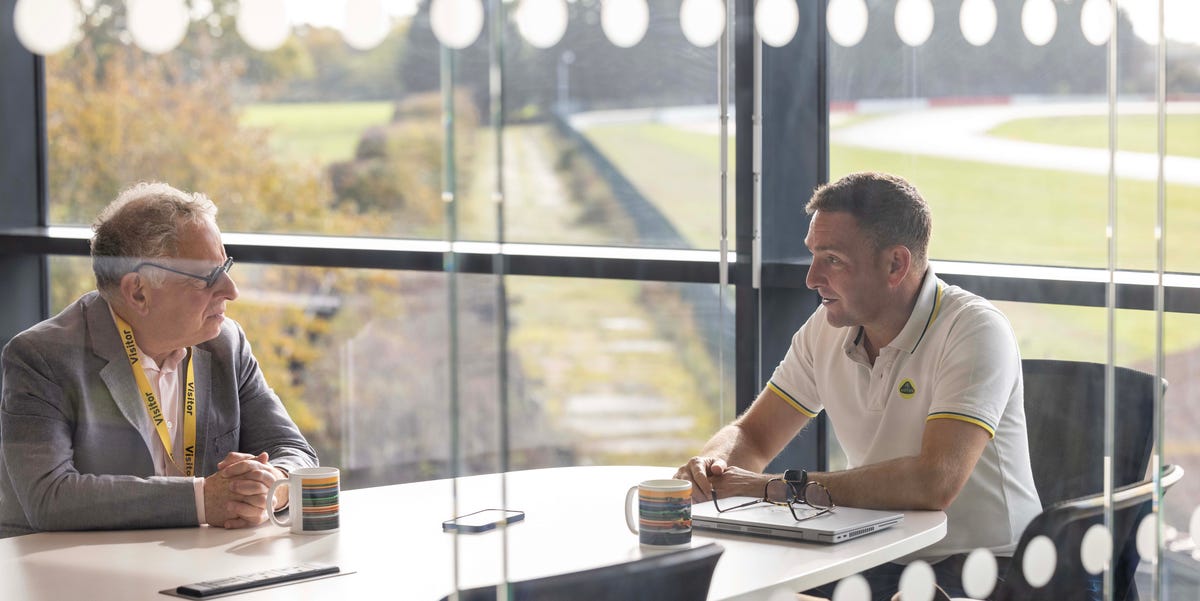
Matt Windle Is Bullish about Lotus's Future Prospects
The specialty carmaker has a new lease on life, and its managing director goes into detail with us about the present and near future.